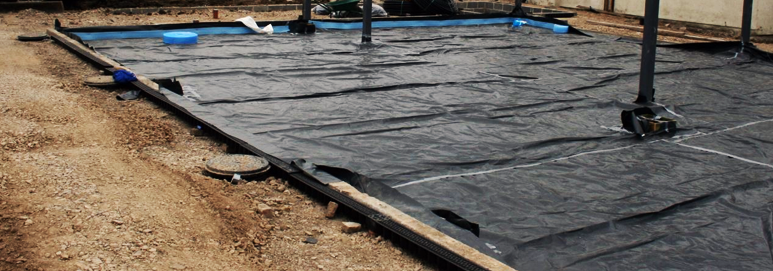
- Damp is a common problem in the UK in many types of buildings and comes in many forms e.g. condensation, rising damp, penetrating damp, hygroscopic damp etc…. When dampness occurs in floors, issues such as insulation impairment, electrical damage and surface damage can occur. The use of highly permeable construction materials such as stone and lime based mortars and renders which were in common use until the 20th century allowed moisture to travel through and be absorbed in to the atmosphere. Problems arose when these materials were covered with new impermeable products such as linoleum, cement, gypsum-based materials and tiles which prevent the dispersion of the moisture causing it to collect just under the surface. These problems may manifest as cracks or expansion and warping of the top floor layer.
2. How can I check if there is moisture in my substrate?
Moisture meters are widely available and will be essential when cleaning and restoring a property after floods as the moisture you can not see will often do the most damage if left undetected and treated.
Before bonding an impermeable floor covering to the substrate it is essential that a moisture test be carried out to ensure the base is sufficiently dry to receive the selected floor covering. It is advisable to use a digital hygrometer that indicates both relative humidity and air temperature.
If you suspect that your damp proof course has failed we recommend that you contact a surveyor or a company specialising in damp problems to inspect your property.
3. What types of damp protection should have been used in the construction of my property?
Incorporating some kind of damp proofing in to buildings only became standard in the 1950s so it is possible that you do not have a damp proof course or that it has deteriorated over time. Common damp proofing techniques include;
- Chemical damp proof course – silicone based liquid is injected in to the wall at no less than 150mm from the base to create a water repelling layer.
- Integral damp proof course – this technique involves adding materials to the concrete mix to make the concrete itself impermeable.
- Membrane damp proof course – a damp proof membrane material such as polyethylene sheeting is placed beneath a concrete slab to prevent it absorbing moisture.
4. How easy is it to install a damp proof membrane?
These days there are some excellent products on the market that make the process of protecting your property from damp relatively quick and easy. If you’ve tested the base over which you want to lay an impermeable floor covering and found moisture in it that will prevent the adhesive from curing and may damage the floor once it’s laid we recommend a product such as Stopgap F77
5. Are there any other solutions?
Yes – use Ecotile! The interlocking tile system allows moisture to evaporate through the joints so damp will never collect between the substrate and the tiles and you can save yourself a lot of time, money and hassle!
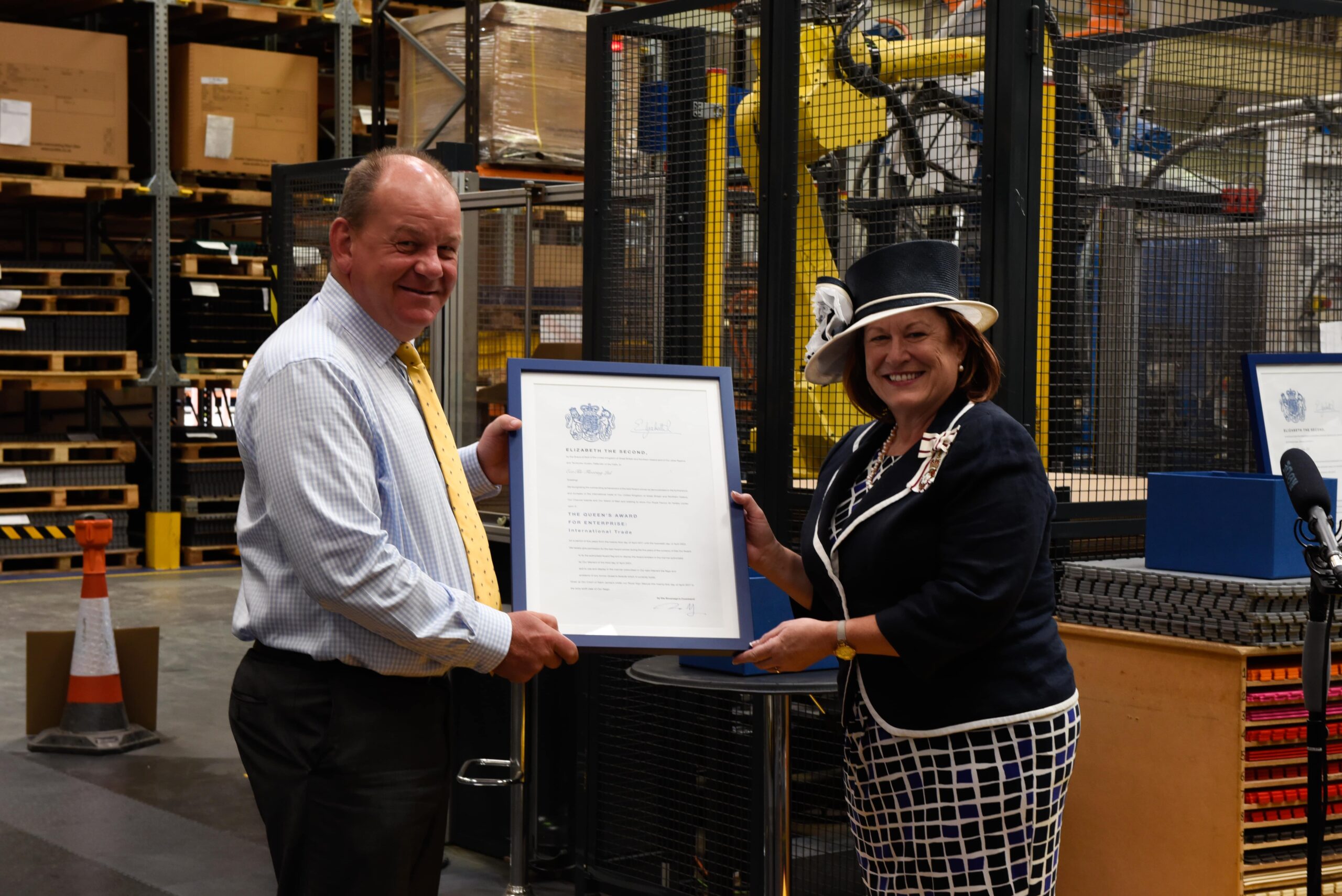
CEO and founder James Gedye has established Ecotile as the leading provider of interlocking floor tiles to the UK and around the world. Founded in 1996 from his bedroom turned office, James has built Ecotile into a multi-million-pound business, with sustainability still at the heart of his vision.
Based in Luton, Bedfordshire, Ecotile remains a privately owned UK manufacturing company, precision engineering all products in a purpose-built ISO accredited factory.
Leading the company to 2 prestigious Queens Awards in 2017 for Enterprise for Innovation and International Trade, these accolades underline James’ desire to create the highest quality products and fly the flag for British manufacturing. Working directly with leading businesses for over 25 years, James’ Ecotile brand has become synonymous with trust.
Used by 1000s of leading businesses, trusted by the MoD and specified by contractors, Ecotile floor tiles can be found across the world.
Connect or follow James on LinkedIn…